Controllability the key to wastewater plants updating their blowers
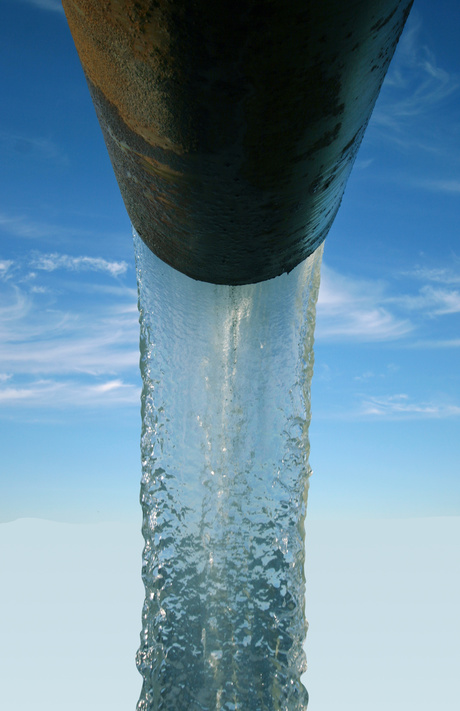
Traditionally, the only options for supplying oxygen to wastewater plants were inefficient lobe blowers or large gear turbo units. That was until Atlas Copco introduced its efficient range of positive displacement screw blowers.
Dennis Benson, Atlas Copco’s business development manager – low pressure, says there are three main factors why Australian wastewater plants are making the switch to screw blowers: controllability, reliability and reduced energy usage.
“We have developed our units to specifically meet the demands of cyclic aeration systems in our extreme climatic conditions,” he said.
He explained that most wastewater plants receive very little sewage during the night — normally about 75% less than during the day. “Therefore, it’s important to offer a blower with a large turndown [80%] to limit the amount of oxygen going into the tanks to suit the demand,” he said.
He added that over-aerating the tanks leads to high ammonia levels and increased smell, and very irate neighbours. “Therefore, a high turndown ability is essential for the smooth operation of a wastewater plant over a full week cycle,” he said.
Even with such a large turndown ability, Benson says it’s sometimes necessary to switch the blower on and off to prevent over-aerating the tanks. “Atlas Copco blowers are designed to start and stop as required many times a day,” he said. “In fact we have blowers regularly stopping and starting 48 times per day, with no reliability problems at all.”
He went on to explain that lobe blowers only have a maximum turndown of 50% and are very inefficient in today’s energy-conscious world. “Because our blowers are of positive displacement design, and equipped with appropriate bearings for the application, they are far more reliable and efficient, reducing energy costs and maintenance,” he said.
Benson said users who have invested in positive displacement screw blowers don’t experience the pulsations and noise going down the lines. Another benefit is the ability to use a smaller motor, doing the same job as a lobe the next size up.
When comparing blowers, Benson warns users to be aware of how airflow is measured by different manufacturers. “Atlas Copco blower units are designed to the same standard as our normal compressors and are guaranteed to give the desired flow to ISO 1217 appendix C Free Air Delivered, unlike other manufacturers who talk about the inlet flow,” he said.
This guarantee is important as it relates to kilograms of oxygen for a certain amount of kilowatts of power. Benson said Atlas Copco is able to guarantee the amount of oxygen its blowers can deliver, as well as the amount of air coming out of the machines.
Benson recommends that organisations that are having problems with their present blower systems should replace them with Atlas Copco’s screw technology. “They will get a far more efficient blower with the extra turndown, the extra flow rate, coupled with far lower energy and maintenance costs,” he said.
“In fact, our machines are designed for up to eight years’ continuous operation, and when they do need repairs, we are able to conduct the repairs on-site.”
As well as fully packaged blowers, with built-in controllers and VSD drives ready to run, Atlas Copco has available stand-alone screw blowers suitable for external VSD drives in motor control centres as installed in a lot of existing plants. The screw blowers can be installed and run with any other technology installed in all wastewater plants.
Phone: 1800 023 469
Kaeser GBS series rotary screw blowers
This range of blowers offers high efficiency and low maintenance and is suitable for applications...
Odosense Odour Emissions Tracking System
Odosense is an active odour analysis and public complaint validation system, which is suitable...
HRS Heat Exchangers C Series heat exchanger
The C Series of industrial multi-tube heat exchangers features a small tube diameter to improve...