Making empty tanks a thing of the past: remote monitoring of tank-filling levels
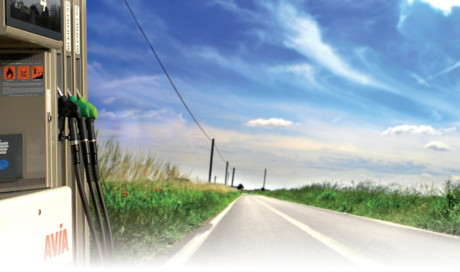
AVIA Osterwalder St. Gallen AG operates more than 120 filling stations in eastern Switzerland. The company also sells and distributes motor vehicle and other fuels to corporate and private customers.
For many years, AVIA Osterwalder St. Gallen AG has deployed the EasyOil@ system to offer their customers a practical method for remote monitoring of filling levels in oil and gasoline tanks. To assist with the recent relaunch of the EasyOil@ system, AVIA Osterwalder St. Gallen AG called on the measurement technology expertise offered by KELLER.
Using a GSM modem to transmit data via mobile telephone network, EasyOil@ is a measurement system used by AVIA Osterwalder St. Gallen AG that offers remote monitoring of the filling levels in the oil and gasoline tank. The contracting customers are alerted via SMS if the tank filling levels fall below a defined limit. This system provides huge advantages to the customers as the filling level data can be downloaded anywhere and at any time, which enables customers to plan their purchase efficiently.
For the EasyOil@ system to work effectively, the sensor technology has to be able to measure filling levels as well as adaptable with the GSM transmission module. With extensive applications in water management sectors, the KELLER pressure probes are technically feasible to be integrated in the EasyOil@ technology as the pressure at specified point in the tank is directly proportional to the filling levels. For AVIA Osterwalder, KELLER developed a GSM-3 variant model to integrate the existing pressure transmitter and SMS communication module.
Cutting-edge technology, intrinsically safe and high-temperature resistance in EX areas
The GSM-3 comprises the modem itself and as many as three pressure transmitters with voltage output of 0.5 to 4.5 V. The circuit also contains three built-in safety barriers, which makes it intrinsically safe to transfer the electrical signals to gas stations. The safety barrier limits the electrical power produced by the measurement system within the area subjected to explosive hazards (EX area). The complete package also includes a level sensor cable to transmit the measurement signals from the tank to the GSM-3 located outside of the EX area.
The 26 Y Ei-series level sensors are intrinsically safe for application in EX-area. The sensors are developed based on the piezoresistive silicon measuring cell, invented and patented by Keller’s CEO and founder, Hannes W. Keller, at the end of the 1960s. The filling level is detected based on the change in resistance in the piezoresistive element caused by liquid pressure. This produces the electrical voltage that is used as the measurement indicator. This sensor is also able to electronically compensate for temperature error, due to ambient or tank condition.
One-stop expertise
Thanks to KELLER’s extensive experience and its highly mature product range, the company can now produce the pressure transmitters for the EasyOil@ system with an excellent cost-to-benefit ratio. These products guarantee long-service lifetimes, even in an aggressive environment, such as gasoline. This is due to their robust stainless-steel housing (IP68 protection), and stainless-steel diaphragm to protect the silicon measuring cell against the fluid.
AVIA Osterwalder St. Gallen AG now purchases either the conventional 26Y level sensor or the intrinsically safe, 26 Y EI-series from KELLER, together with the GSM-3 transmission unit and sensor cable. The final system assembly and installations at the customers’ premises and software configurations are managed by AVIA Osterwalder themselves. Overall, the project receives positive response.
Bestech, the sensor technology and teaching equipment specialists, is the partner and distributors of KELLER’s technology in Australia. The application engineers at Bestech are highly trained with specific product knowledge and have demonstrated the capability of KELLER’s products in numerous applications.
Case Study: Nordfab Pty Ltd x Green-Technology, E-Waste Company
Implementing Nordfab Australia's packed tower wet scrubber, ducting system, and carbon filter...
Case Study: Nordfab Dust Extraction System for a Glass Recycling and Resource Recovery Company
Nordfab Pty Ltd engineered a dust extraction system for a glass recycling and resource recovery...
Putting waste to good use: harnessing the power of biosolids
Solid waste management is a crucial yet overlooked factor in achieving a circular economy.