Old clothes turned into building materials
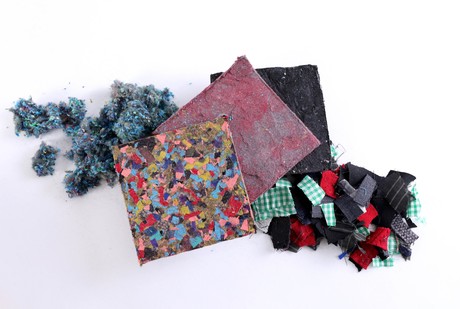
UNSW researchers have developed a process to turn old clothing and textiles into high-quality building products such as flat panels, which have been lab tested for qualities such as fire and water resistance, flexibility, acoustics and load-bearing capabilities.
This follows a separate but related exercise that converted used glass into high-quality ceramics suitable for benchtops and tiles in kitchens and bathrooms that can come in all sorts of sizes, colours and finishes.
Led by Professor Veena Sahajwalla, Director of UNSW’s Centre for Sustainable Materials Research and Technology (SMaRT Centre), researchers have been scientifically reforming common waste items using prototype technology developed for a laboratory-scale ‘green microfactory’. Prof Sahajwalla noted that, considering that the world’s population is expected to jump from 7.6 billion to 9.8 billion by 2050, the Earth’s resources need to be preserved and re-used rather than put in landfill or incinerated.
“It could be said that consumers and the fashion industry have a lot to answer for, given that clothing is now one of the biggest consumer waste streams, with 92 million tons estimated to be thrown out a year globally,” she said. “The clothing and textiles industry is the second-most polluting sector in the world, accounting for 10% of the world’s total carbon emissions.”
Reforming old clothing and mixed waste glass into various high-quality building products represents a new way to convert low-value waste into high-value products and materials. This work builds on technology which can recover and reform materials from electronic waste at UNSW’s demonstration e-waste microfactory, launched by NSW Environment Minister Gabrielle Upton in April 2018.
The demonstration microfactory showcases a process developed by the SMaRT Centre which transforms the components of discarded electronic items like mobile phones, laptops and printers into new and re-usable materials that can then be used to manufacture high-value products such as metal alloys, carbon and 3D printer filament. Prof Sahajwalla said green microfactories not only produce high-performance materials and products, they eliminate the necessity of expensive machinery, save on the extraction from the environment of yet more natural materials and reduce the waste burden.
“There is much that can be done right now given that scientifically developed, proven methods are currently available through our green microfactory technology,” she said. “Rather than export our rubbish overseas and to create more landfill, green microfactory technology has the potential to enable small- and large-scale creation of newly manufactured products instead.”
UNSW is now finalising a second demonstration green microfactory which converts glass, plastics and other waste materials into value-added products. Mixed waste glass is used to create engineered stone products, while wood, plastic and textile waste is used to create valuable insulation and building panels. These high-end composite products can have a wood veneer look or a ceramic-style finish.
The textiles materials have already tested well for mechanical performance properties including strength, flexibility and resistance. Further lab testing is required to explore these properties ahead of consideration of applying for any formal assessment against construction regulations.
Please follow us and share on Twitter and Facebook. You can also subscribe for FREE to our weekly newsletter and bimonthly magazine.
REDWAVE TEX textile sorting solution
The REDWAVE TEX is a flexible sorting solution designed specifically for the textile industry.
PCO.Tech pco.pixelfly 1.3 SWIR camera
The pco.pixelfly 1.3 SWIR is a machine vision camera with an InGaAs image sensor that is...
Emi Controls V12so Odour Control Cannon
The V12so Odour Control Cannon combines four different functions in one machine — eliminate...