Improved sorting system for recycling facilities
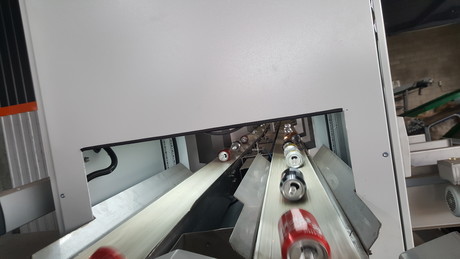
Container Deposit Systems Australia (CDSA), which harnesses technology to improve productivity within recycling depot facilities, recently approached SAGE Automation with an unusual automation challenge.
Recent environmental legislation has seen many recycling plants face reduced efficiencies and increased costs due to the purchase of expensive sorting machines from Europe, coupled with expensive, unreliable labour. With these sorting machines relying on barcodes, waste is of major concern as damaged products cannot be read.
The NSW Environmental Protection Authority’s Return and Earn scheme in particular has come under fire for accepting only ‘perfect rubbish’, with the Return and Earn website saying “containers should be empty, uncrushed, unbroken and have the original label attached”. All of these factors put a strain on CDSA’s customer satisfaction.
“We position recycling facilities to realise significant productivity gains, improved customer relationships and highly secure and auditable product management,” said CDSA Executive Chairman Brett Duncanson.
“Priding ourselves on customer satisfaction, the issues that we were facing were hindering our business and we were turning customers away rather than making them want to take on the task of recycling and collecting money.”
SAGE Automation worked closely with its automation partners, such as drive technology supplier NORD DRIVESYSTEMS, to improve efficiencies through better accuracy. The company developed a range of counting and sensing technologies to determine the container types being retained — even when containers were not in their original condition. Answering to the calls for IoT technology, the system provides valuable data which is delivered into the cloud and used for reporting.
At the heart of the machine is the vision system, provided by the University of South Australia (UniSA). The camera uses an algorithm to identify what each item is and sorts them into the correct skid. This includes not just identifying cans and bottles, but also colour.
“SAGE incorporates various component suppliers into an integrated solution for customers,” said SAGE Automation general manager of operations Paul Johnson. “The challenge with CDSA’s request was that the plant was already operational and the customer required that the solution be installed easily and very quickly on-site. It also had to require minimal maintenance and provide intelligence about the facility operations.
“We looked for ways to simplify the installation. Five skids with 26 conveyors needed to be installed within a day, so we looked to a ‘plug and play’ solution to get it up and running as fast as possible.”
A distributed drive solution was used to achieve the brief. It required a 240 V drive which used EtherCAT and could be Beckhoff integrated. SAGE partnered with NORD DRIVESYSTEMS, the only company it found that could provide this solution.
“We hadn’t worked with NORD previously and we were really impressed with the way that the team listened to what we wanted,” said Johnson. “They understood our needs and their engineering team configured the unit to ensure seamless integration with Beckhoff — literally overnight!
“The solution was exactly what we wanted and the local stockholding, price point and engineering expertise sealed the deal. The products used were of the highest quality and latest technology. The motor gearbox drive is distributed so that the inverter sits on top of the gearbox and it is neatly daisy-chained together.”
In the end, SAGE Automation was able to install 26 conveyors with five skids in just one day.
With the second prototype underway and recognising the formation of what hopes to be a fruitful and strengthened partnership, NORD DRIVESYSTEMS Sales Manager for the region Vinod Pillai looks forward to more exciting projects with SAGE Automation.
“It’s an honour to be associated with a South Australian-founded company such as SAGE Automation,” said Pillai. “SAGE is known across the industry for its expertise and quality, and we hope that this is the beginning of a very successful partnership.
“NORD’s decentralised solution looks to modular assembly for ease and reduced downtime during component failure. It also offers a decentralised inverter which is economical and robust. The site did not have access to three-phase power, and as such the project made use of a Nordac base — a single-phase input supply option for 0.25 to 1.5 kW.”
NORD also managed to engineer plug connector solutions for both power supply and EtherCAT connection.
“In keeping the footprint compact, the Nordac base offers assembly of an internal EtherCAT fieldbus card,” said Pillai. “The flexibility of being able to assemble dual plugs on the Nordac Base for both power supply connection as well as M12 connectors that enabled fieldbus communication in turn allowed for simple daisy-chain topology to be realised for the inverter modules.”
The new development comes just ahead of the national legislation rollout of the new government recycling program. It places CDSA in the position of being able to help recycling plants to be up and running and ready for the new program in no time.
“We are more than pleased with the solution and are currently busy with the second prototype,” said Duncanson. “What we do is extremely important to both our customers and the environment. The solution supplied by SAGE Automation and its partners will make a big difference to our customers by helping to improve productivity.”
Phone: 03 9394 0500
REDWAVE TEX textile sorting solution
The REDWAVE TEX is a flexible sorting solution designed specifically for the textile industry.
PCO.Tech pco.pixelfly 1.3 SWIR camera
The pco.pixelfly 1.3 SWIR is a machine vision camera with an InGaAs image sensor that is...
Emi Controls V12so Odour Control Cannon
The V12so Odour Control Cannon combines four different functions in one machine — eliminate...