Smart solutions enabling smarter operations
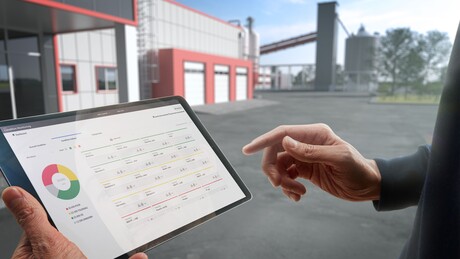
It’s no secret — all operational managers are intensely aware of the urgent need for smarter efficiency. As complexity of managing electrical assets increases across facilities of every size, ensuring reliability of such equipment in the long term becomes crucial both in terms of health of this equipment and in terms of consistent cost saving that this equipment would require while running and in service.
A forward-thinking approach in conducting maintenance practices and optimisation strategies must be adopted to meet such requirements.
When it comes to meeting operational complexity head on, your facility’s data is your greatest ally. By transforming data into actionable insights, you can uncover opportunities for improvement, mitigate risk and create more sustainable processes.
Though many are wary of introducing more complexity into operations, the fact is that it’s never been easier to harness data that supports your expertise.
How can data help me prioritise maintenance actions?
By clearly communicating asset performance and identifying what needs most urgent attention.
- Deep dive: Explore each asset’s diagnostics and prognostics and view condition indicators for relevant components eg, environmental, electrical, dielectric, mechanical and thermal.
- Check condition labels: Diagnostic algorithms clearly designate each asset’s condition, labelling assets from ‘Very poor’ (mostly failed, urgent action required) to ‘Very good’.
- Prioritise: Based on condition indications, you can efficiently assign maintenance where there is a higher probability of failure and criticality.
How can data help me predict faults?
By letting you combine historic information with real-time analytics.
- Continuous condition monitoring: Sensors constantly monitor for the possible failure causes in your assets. It means you can track things like electro-mechanical performance in circuit breakers and monitor temperature/environmental parameters without having to regularly halt production.
- Actionable insights: Used in combination with sensor data, analytics can highlight potential abnormal conditions before failure occurs, eg, alerting operators if trends indicate temperature could rise above a safe threshold. Moving towards predictive maintenance means you’re always one step ahead, avoiding high-cost unplanned labour and maintenance and extending asset lifetimes by up to 15%.
How can data empower my team and keep them safe?
By letting you communicate real-time insights to your people, wherever they are.
- Real-time updates: Keep operators safe from anywhere with up-to-the-minute insights and data notifications. This allows them to plan in advance, take appropriate action faster and observe the right safety precautions.
- Remote scheduling: Analytics and insights allow you to streamline maintenance planning, assign field service and track activities/reporting, so everyone can see exactly what they’re doing.
Without your knowledge and expertise, data and insights are nothing but figures on a screen. Data is undeniably powerful but it’s your asset management strategy that determines whether assets boost or create a drag on business results.
By placing data at the foundation of your strategy, an asset management solution brings tangible benefits to operations. Its functionality actively extends your insight, acting as your eyes and ears across your entire facility.
Through digital asset management technologies, such as ABB Ability™ Energy & Asset Manager, giving you access to data across asset health, events and alerts, maintenance prescription and documentation, it’s truly never been easier to unlock your site’s potential and power a more sustainable future.
Navigating asset transitions for a sustainable and equitable future
Closing major assets like power stations or mines can profoundly impact local communities....
Digital divide threatens corporate journey to net zero
A deep digital divide is emerging in corporate approaches to sustainability, potentially...
The Pressure to Report
These days, businesses are no longer just accountable to their customers or a single owner.