Measurement of Dewpoint in Industrial Gases
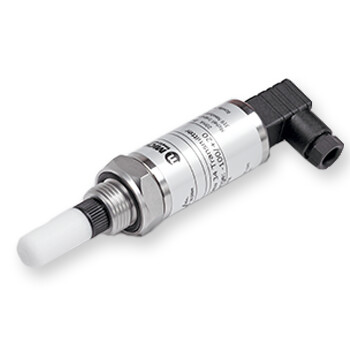
Measurement of dewpoint in industrial gases is a strength of Michell Instruments and AMS. However, it is good to know some basic rules about “Good Measurement Practice” for this important KPI.
Good Measurement Practice
Michell manufacture a vast range of devices to monitor dew point. As you would expect from experts, their equipment is designed for all types of application. From the ‘simple’ Dew Point Transmitter to sophisticated Chilled mirror; Quartz resonance; and Tunable Diode Array, Analysers.
Moisture measurement is seen in many, many industries and applications. If we focus on the ‘simple’ Dew Point Transmitter to start. The measurement ‘cells’ of these are generally solid state devices built of ceramics and base metals. Often they are designed to operate in a flowing gas stream and they are suitable for the measurement of the moisture content of a wide variety of gases. In general, if the gas (in conjunction with water vapor) is not corrosive to ceramics or base metals then it will be suitable for measurement.
These transmitters, while not ‘looking’ like it, are still an analyser so the next question is, how do we get them into the gas or get the gas to them?
Sampling Considerations
There are two basic methods of measuring a sample with a dew point transmitter, such as Michell’s Easidew, SF82 or one of the packaged systems based around these transmitters:
- In-situ measurements are made by placing the transmitter inside the environment to be measured.
- Extractive measurements are made by installing the sensor into a block within a sample handling system, and flowing the sample outside of the environment to be measured through this system.
Extractive measurements are recommended when the conditions in the environment to be measured are not conducive to making reliable measurements with the product.
Examples of such conditional limitations are:
- Excessive flow rate
- Presence of particulates matter
- Presence of entrained liquids
- Excessive sample temperature
The basic considerations for each measurement type are as follows:
In-Situ
Dew-Point Sensor Position — will the sensor see an area of the environment that is representative of what you want to measure?
For example, if the sensor is to be mounted into a glove box, there are three different positions in which it could be installed — each giving a different measurement:
- Position A is on the purge inlet. In this position the sensor will confirm the dew point of the gas entering the glove box, but will not detect any leaks in the glove box itself, or any moisture released from the work piece.
- Position B is on the gas outlet. In this position the sensor will be exposed to the gas leaving the glove box, and will therefore be detecting any moisture which has entered into the system (e.g. ingress/leaks), or has been released by the work piece.
- Position C is in the glovebox itself, in this position the sensor will be only detecting any moisture in its immediate vicinity. Leaks not in close proximity to the measurement point may not be detected as this moisture could be drawn directly to the outlet.
If the transmitter is to be mounted directly into a pipe or duct, then consider that the installation point should not be too close to the bottom of a bend where oil or other condensate may collect.
When installed directly into a process line, velocity should be kept below 10m/s. When taking a sample there are many things to consider (see below) but in general a flow of between 1 and 6Nl/min fit. In either installation care must be taken with the gas being presented to the Dew Point sensor.
Flow Rates
Theoretically flow rate has no direct effect on the measured moisture content, but in practice it can have unanticipated effects on response speed and accuracy.
An inadequate flow rate can:
- Accentuate adsorption and desorption effects on the gas passing through the sampling system.
- Allow pockets of wet gas to remain undisturbed in a complex sampling system, which will then gradually be released into the sample flow.
- Increase the chance of contamination from back diffusion: ambient air that is wetter than the sample can flow from the exhaust back into the system. A longer exhaust (sometimes called a pigtail) can also help alleviate this problem.
- Slow the response of the sensor to changes in moisture content.
An excessively high flow rate can:
- Introduce back pressure, causing slower response times and unpredictable effects on equipment such as humidity generators.
- Extremely high gas speeds can cause damage to the sensor.
Extractive
For samples the main objective of any Sample Handling System is to get a representative, timely, clean sample to the measurement point. With that in mind flow rates; particulate loading; length of tubing; type of tubing and expected dew point; ambient temperature range; process temperature range; are all important.
In the meantime —
isn’t it time to be more Analytical!
For further information contact AMS Instrumentation & Calibration Pty Ltd on 03-9017 8225, or Freecall (NZ) 0800 442 743, alternatively on e-mail: sales@ams-ic.com.au or visit our web site at www.ams-ic.com.au.
STABILISOR tech revolutionises air compressor operation
ELGi's STABILISOR technogy sets new standards in compressed air reliability, energy costs and...
Digital divide threatens corporate journey to net zero
A deep digital divide is emerging in corporate approaches to sustainability, potentially...
Navigating asset transitions for a sustainable and equitable future
Closing major assets like power stations or mines can profoundly impact local communities....