Protective coatings based on potato starch
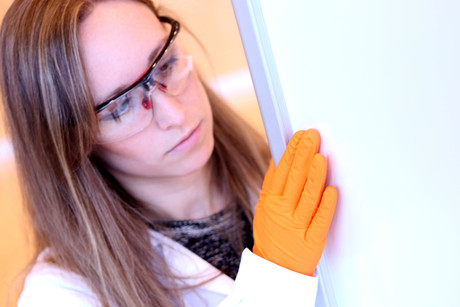
Researchers at the Fraunhofer Institute for Applied Polymer Research IAP, in cooperation with the Fraunhofer Institute for Manufacturing Engineering and Automation IPA, are developing a cost-effective surface coating based on renewable raw materials. The focus of their research? Potato starch.
More and more industries are focusing on sustainable production, including the production of coatings such as paints and varnishes for protection against corrosion. In the past, however, coatings with bio-based binders or film formers have either been too expensive or could not sufficiently meet requirements. Now, through the use of modified starch, scientists at the Fraunhofer IAP have found a way which even in this field makes sustainable and cost-effective solutions possible.
“Until now, traditional industrial fields of application of starch have been the paper/corrugated cardboard and adhesives industries,” said Christina Gabriel, a scientist at the Fraunhofer IAP. “In the field of paints and varnishes on the other hand, starch was usually only used as an additive. With starch as the main component of a water-based dispersion, we now have very promising adhesion results.”
At the centre of the research is the coating of metals for indoor use, for example aluminium, which can be used for fire doors, computer housings or window frames. Here, the use of starch as the main component of paints and varnishes posed various challenges to the scientists.
“Film formers must fulfil several tasks,” said Gabriel. “They must form a continuous film, which adheres well to the substrate material, is compatible with additional layers and additives, and can embed pigments and fillers as well.
“In its natural form, however, starch exhibits several properties which stand in the way of its use as a film former. For example, it is not soluble in cold water and neither does it form continuous, non-brittle films. We therefore had to modify the starch to adapt it to the requirements as, in spite of all the challenges, as a renewable and cost-effective raw material, starch is of great interest for many sectors.”
The scientists’ solution involved an initial degradation step of the starch in order to improve its solubility in water and the subsequently associated solids content of the starch in water, as well as its film forming ability. However, in order to produce a starch-based coating material, which is comparable with a conventional coating, this is not yet sufficient. Although the film former should initially be soluble or dispersible in water, the coating must subsequently no longer dissolve in water. The starch must therefore be modified further.
This modification takes place by way of a chemical process known as esterification. The resulting starch esters are dispersible in water, form continuous films and have very good adhesive properties on glass and aluminium surfaces. The esterified starch is then ‘cross-linked’, through which the sensitivity of the coating to water is reduced further. The stability tests to check the long-term stability are then carried out.
In these tests, the coated materials are exposed to rapidly changing temperature cycles in a time-compressed form to simulate the change from day to night and the course of the seasons. In addition, the test objects are exposed to electrolyte-enriched water in order to see how the coating reacts to water and how resistant it is under extreme conditions.
In the next step, the resistance to corrosion and adhesion of the modified starch on different metal substrates is examined. New ‘recipes’ are also being tested, which are intended to optimise the properties of the coating even further.
“Apart from the already tested aluminium, two other important metals, steel and galvanised steel, are to be tested,” said Gabriel. “Our investigations show that with its good film forming and very good adhesion properties on various substrates, starch esters have the potential to be future alternatives to petroleum-based film formers in the coatings industry.”
Vertiv CoolLoop Trim Cooler
The Vertiv CoolLoop Trim Cooler is designed to operate with fluctuating water temperatures...
Ecoforest heat pumps
Suitable for a wide range of building sizes and applications, Ecoforest heat pumps offer scalable...
Thermo Fisher Thermo Scientific ARL iSpark Plus optical emission spectrometer range
The Thermo Fisher spectrometer range is designed to streamline elemental analysis in...