Diamond-like coatings help save fuel
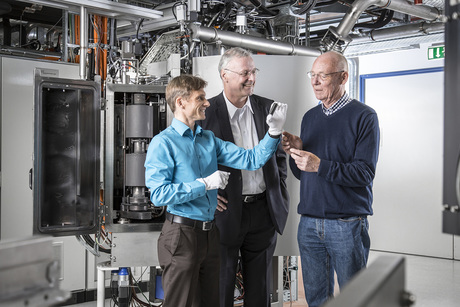
Researchers from the Fraunhofer Institute for Material and Beam Technology IWS have developed a new method for reducing the friction generated by engine components to almost zero — a breakthrough that could save billions of litres of fuel worldwide every year.
Scientists already know how to coat components with carbon, with Fraunhofer researcher Professor Andreas Leson noting that the material’s “low friction and high resistance to wear are the key qualities we exploit in practical applications”. But while tetrahedral amorphous carbon (ta-C) coatings are even more resistant to wear than conventional diamond-like coatings, researchers have been unable to produce the material on an industrial scale — until now.
“Unfortunately, you can’t just scrape off diamond dust and press it onto the component,” said Dr Hans-Joachim Scheibe. “So we had to look for a different method.”
The method in question was the development of pulsed laser which generates an arc between an anode and a cathode (the carbon) in a vacuum. The arc is initiated by a laser pulse on the carbon target. This produces plasma consisting of carbon ions, which is deposited as a ta-C coating on the work piece in the vacuum. The system can be connected to existing coating machines.
To run the process on an industrial scale, a pulsed laser is vertically scanned across a rotating graphite cylinder as a means of controlling the arc. The cylinder is converted evenly into plasma thanks to the scanning motion and rotation. To ensure a consistently smooth coating, a magnetic field guides the plasma and filters out any particles of dirt.
The laser arc method can be used to deposit very thick ta-C coatings of up to 20 µm at high coating rates. As explained by team member Dr Volker Weihnacht, “High coating thicknesses are crucial for certain applications — especially in the auto industry, where components are exposed to enormous loads over long periods of time.”
Automotive and motorcycle manufacturer BMW is currently working on the industrial-scale implementation of ta-C engine components, such as piston rings and pins, in its various vehicle models. According to BMW representative Dr Franz-Josef Wetzel, the resulting improvement of vehicle performance and acceleration on the road “can mean a double-digit per cent reduction in fuel consumption”.
“The coming decade will see the European Union introduce even stricter regulations on CO2 emissions, so friction reduction would obviously be one of the methods we use to meet the new targets,” Dr Wetzel said. “Systematic use of low-friction coatings could save up to 117 billion litres of fuel a year over the next 10 years — equivalent to 290 million tonnes of CO2 emissions.”
Professor Leson, Dr Scheibe and Dr Weihnacht received the 2015 Joseph von Fraunhofer Prize for their development of the laser arc method and the application of ta-C coatings in volume production.
Ecoforest heat pumps
Suitable for a wide range of building sizes and applications, Ecoforest heat pumps offer scalable...
Thermo Fisher Thermo Scientific ARL iSpark Plus optical emission spectrometer range
The Thermo Fisher spectrometer range is designed to streamline elemental analysis in...
Nordfab Quick-Fit Ducting
Quick-Fit (QF) Ducting is designed to ensure that work environments are comfortable and conducive...