The Impact of High-Efficiency Mechatronic Drive Systems on Energy Reduction
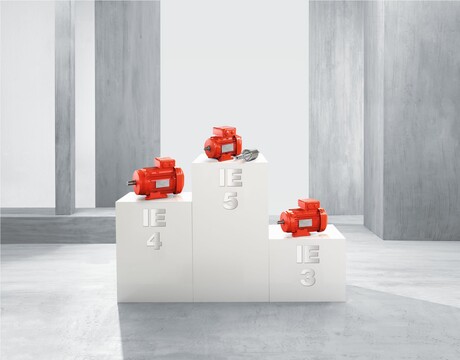
In an era where energy conservation is paramount, high-efficiency mechatronic drive systems are emerging as vital components in various industries. These systems combine mechanical, electrical, and electronic engineering principles to enhance performance while minimizing energy consumption. As businesses seek to lower their operational costs and environmental impact, the adoption of these advanced technologies are becoming increasingly crucial.
The question then becomes, what is the best way to adopt these technologies in industrial applications? Francois Sieberhagen, National Product Engineer – Product Management at SEW-EURODRIVE, says that optimising the entire drive system leads to significant improvements. He says that the energy expenses associated with operating electric motors may account for more than 80% of the total cost of ownership (TCO).
Sieberhagen suggests focusing on optimising the efficiency of each component in the drive chain to ensure that they all have high energy efficiency ratings, both individually and as a system. He explains that two prevailing international standards govern the efficiency of electric motors.
IEC 60034-30-1 covers line-operated AC motors. The standard refers to efficiency classes from IE1 to IE4, with IE1 – Standard Efficiency being the least efficient and IE4 – Super Premium Efficiency the most efficient.
IEC TS 60034-30-2 specifies efficiency classes for inverter duty motors not covered by IEC 60034-30-1. This standard introduces an additional efficiency class, IE5 – Ultra Premium Efficiency, which is currently the highest defined class.
Exceeding the standard
In Australia, MEPS regulations mandate that low voltage motors meet a minimum energy performance standard of IE2, which is classified as high efficiency. Sieberhagen notes that the motors supplied by SEW-EURODRIVE to the Australian market not only meet but surpass this requirement, with efficiency classes ranging from premium (IE3) to ultra-premium (IE5).
MOVIGEAR® performance combines the motor, gear unit, and frequency inverter into a single, compact housing, with integrated communication for operation on all standard Ethernet-based infrastructures. This innovative drive unit is notable for its space-saving design, impressive overload capability and it is up to 50% lighter than conventional drive systems. By combining the inverter with IE5-class motors, MOVIGEAR® performance surpasses the highest defined energy efficiency class IES2 to IEC 61800-9-2 for systems comprising of a motor and inverter, setting a new benchmark that outperforms current market solutions. These products are often used for dynamic material handling applications. In Europe, one fulfilment centre achieved 1710 kg/year fewer CO2 emissions and a 57% average energy saving per drive after modernising with a MOVIGEAR® performance solution. They were also able to reduce noise by 50% due to the drives being fan-free.
The local experience is similar. “A number of Australian airports have achieved energy savings in their baggage-handling conveyor lines by installing MOVIGEAR® performance. The extent of the improvement ranges from 50% to 70%,” says Sieberhagen.
A versatile solution for any application
Other components in the drive system also play a role in reducing energy consumption. SEW-EURODRIVE’s DR2C series synchronous motors also meet the requirements of the IE5 efficiency class. These motors, designed for pure inverter operation, offer dynamic and thermal reserves for a sustainable operation and lifecycle cost reduction. Interior permanent magnet (IPM) technology reduces the size of the motors.
“A DR2C series motor can be two sizes smaller than its equivalent asynchronous motor,” says Sieberhagen.
Sieberhagen also points out that the operating temperature of the DR2C motor has a role to play in contributing to the sustainability of the system. Since the motor runs cooler, it lasts longer. The longer lifetime is once again suitable for both the environment and the bottom line.
Another component to be optimised in materials-handling applications is the drive unit. The SEW-EURODRIVE MOVIMOT® advanced drive unit combines an asynchronous motor with a frequency inverter to create a decentralised drive unit that can be combined with any standard gear unit. Depending on the choice of motor, the efficiency rating will be either IE5 or IE3. Nominal power ratings for drives with the ultra-premium efficiency DR2C series synchronous motor range from 0.75 kW to 2.4 kW; for the DRN series, the range is 0.37 kW to 7.5 kW.
“Further, motors operated with inverters can reduce the energy consumption by adjusting the motor speed to precisely match the application requirements,” says Sieberhagen.
Overall efficiency
Sieberhagen says that maximising energy efficiency relies not just on the individual components but also on the exact way they coordinate with each other. When these components are designed to be a perfect fit, the optimisation is complete. The interplay between cutting-edge electronics and closed-loop control technology on the one hand, and an optimised high-efficiency motor and efficient helical gear unit on the other, culminates in system savings of up to 50% compared to the standard alternative.
Adopting high-efficiency mechatronic drive systems is a transformative approach to energy management across various industries. These systems significantly reduce energy consumption, minimise waste, and enhance operational performance. Consequently, they not only lower operating costs but also contribute to a more sustainable future. As businesses continue to embrace these technologies, the potential for energy reduction and environmental stewardship will undoubtedly grow, paving the way for a greener industrial landscape.
2024 Solar Installation Report Reveals Environmental Impact and Sustainability Metrics Across Australia
The report quantifies Australia's sustainability progress through detailed installation...
Energy Efficiency as an Imperative Climate Strategy
With mandatory climate statement disclosure rolling out in Australia, businesses need to start...
Flow control for optimising growth of microorganisms
Today, more than ever, enzymes and microorganisms are being used to increase sustainable production.