Cheese company cuts energy costs
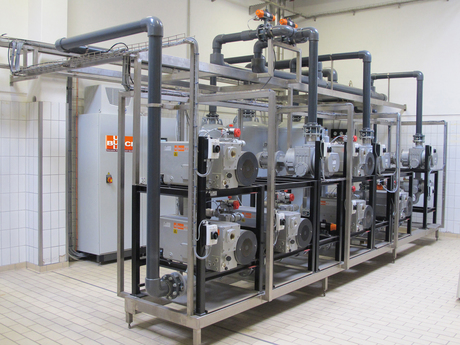
DMK Deutsches Milchkontor is one of the largest dairy companies in Germany, manufacturing 6.7 million tonnes of dairy products per year. The company conducts its energy management according to ISO 50001 standards, leading to a reduction in its vacuum system energy consumption with the introduction of a centralised vacuum system from Busch.
One of DMK’s 28 sites is a production facility in Georgsmarienhütte, which mainly manufactures cheese in packaged portions. At the facility, various types of sliced cheese are packaged in three packaging lines by thermoforming machines. Two additional thermoforming machines package mozzarella in 2.5 and 10 kg blocks for further processing by customers.
All five thermoforming machines originally had two vacuum pumps each: one to form the foil into the mould and one to extract air from the packaging chamber. DMK Energy Manager Yvonne Gödeker wished to reduce the number of vacuum pumps and relocate them away from the production area, whose air conditioner was having to combat the heat emitted by pumps.
Busch recommended the installation of a centralised vacuum system, which was commissioned in October 2014. After a year of operation, the centralisation of the vacuum system had saved about 100,000 kW/h, reducing DMK’s energy costs by approximately €15,000. A major factor behind this was the vacuum control system: only the vacuum pumps needed to meet current demand are in operation.
Vacuum is supplied to the facility by a pipework system with three vacuum circuits: rough vacuum, medium vacuum and forming vacuum. A controller maintains the required vacuum level in all three circuits, matching the demand created by the individual packaging lines. Vacuum pumps are switched on or off as required, maintaining the desired pressure in the vacuum reservoirs. The three packaging lines rarely require maximum pumping speed simultaneously.
The centralised vacuum system is located in an intermediate floor above the production and packaging areas. The relocation of vacuum pumps installed directly to the packaging machines prevents emitted heat from reaching the packaging machines and production area, and no warm air from vacuum pump exhausts is given off to air-conditioned rooms. This has reduced the cooling required by the packaging machine tools, and air-conditioning costs are also lower.
Phone: 03 9355 0600
VECOW AIC-110 IoT gateway
Backplane Systems Technology is pleased to present VECOW’s AIC-110.
Bonfiglioli 700TW Series planetary gearbox
The Bonfiglioli 700TW Series planetary gearbox is the company's new-generation Yaw Drive...
Tindo Walara series N-Type solar panels
Tindo's Walara Series of solar modules is designed for the Australian climate using n-type...